When it comes to customizing the motor control of ebikes or escooters, there is one term you will inevitably encounter: motor field weakening. In this post, I aim to demystify this technique.
TL;DR: The top speed of an electric motor depends on the motor’s windings and the sophistication of its controller. If the controller can implement back EMF weakening, also known as field weakening, you can increase the top speed by 5-10%.
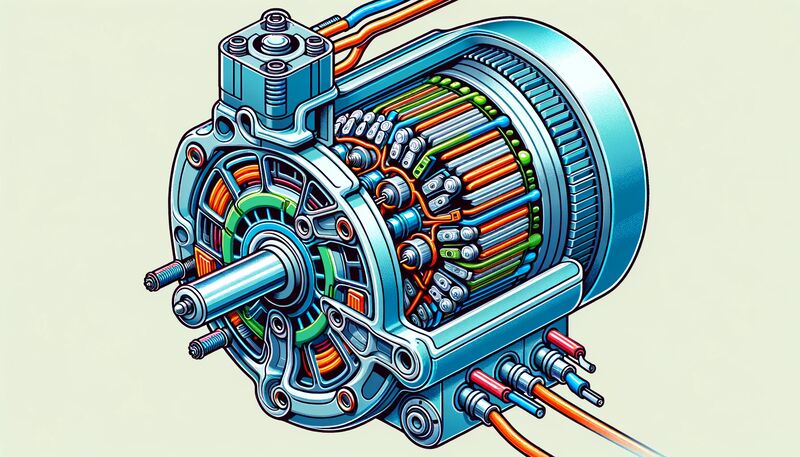
What is Field Weakening?
Field weakening is a motor control technique that enables an electric motor to operate at speeds beyond its rated maximum.
This is achieved by reducing the magnetic field within the motor’s stator. Lowering the magnetic field intensity results in a decrease in back electromotive force (EMF), thus allowing the motor to reach higher rotational speeds.
Although it might seem like a modern technique, field weakening has historical roots. It originated with early electric motors, designed to address the issue of motors that could only operate at a single speed. This was particularly relevant for applications like electric trains. Over time, advancements in motor control have refined field weakening, making it more versatile and applicable to a broader range of uses. In the context of railways, field weakening is sometimes referred to as “field shunting.” [1]
Motor Control Overview
When designing an electric drive system or powertrain, several parameters must be balanced to optimize cost, performance, and thermal management. Key factors include maximum speed, battery voltage, and torque.
For consumer applications, such as ebikes and escooters, there are common speed limits based on the market:
Vehicle | EU | US |
---|---|---|
Ebike | 25 km/h | 32.2 km/h (20 mph) |
eScooter | 20 km/h – 25 km/h | 32.2 km/h (20 mph) |
These limits typically define the top speed for which a motor is designed in these applications, which directly correlates to the battery voltage.
Let’s explore how these elements come together, using a drive system with the advanced motor simulation tool by Grin.
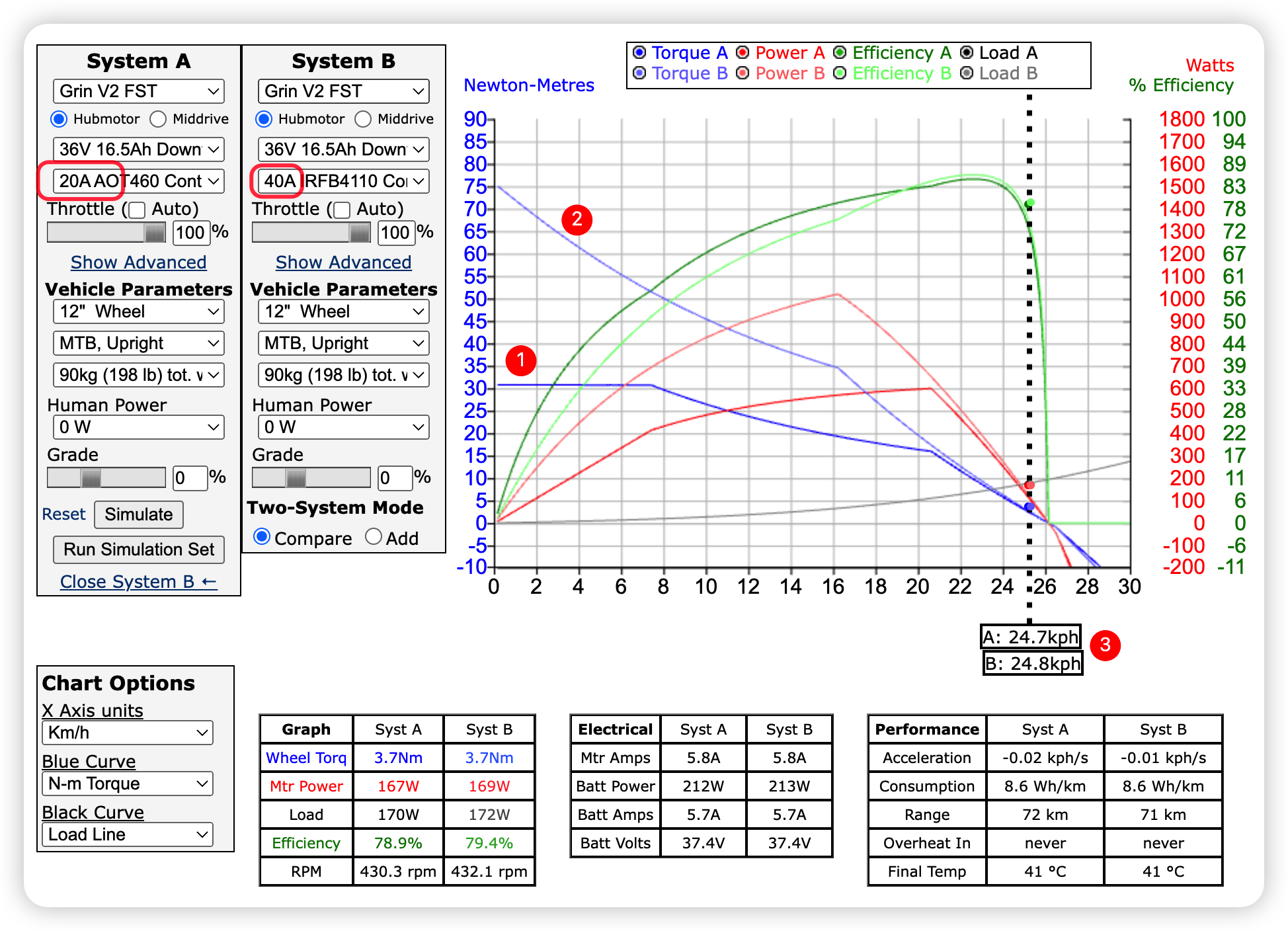
This setup simulates what an eScooter or eBike configuration might resemble in real life.
We observe two identical systems, differing only in one aspect: System A’s maximum amperage is set to 20A, while System B’s is set to 40A. The black curve represents the load, which increases quadratically due to air resistance at higher speeds.
Many people attempt to increase their system’s speed by adjusting this parameter first. However, an interesting lesson emerges from this experiment. Increasing the allowed amperage does not raise the motor’s top speed, which is largely determined by the applied voltage. Instead, what you gain is more torque. But, it’s important to remember another rule of thumb:
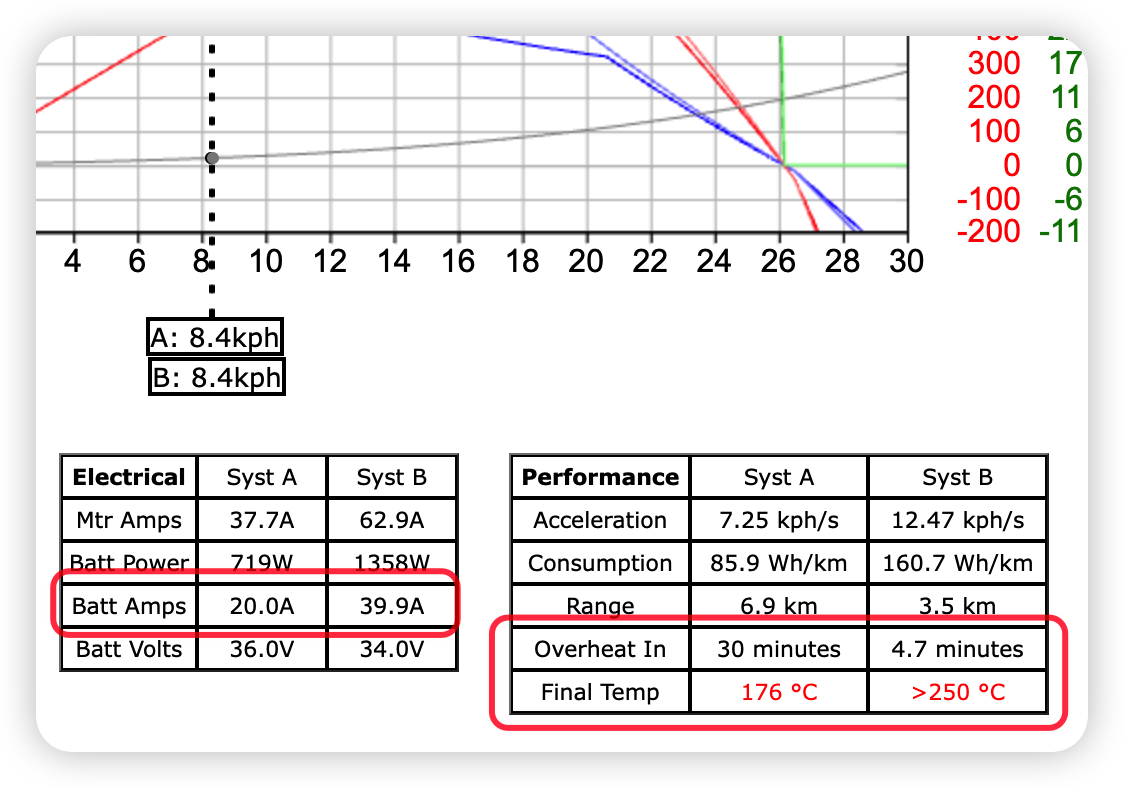
Doubling the amperage quadruples the thermal stress.
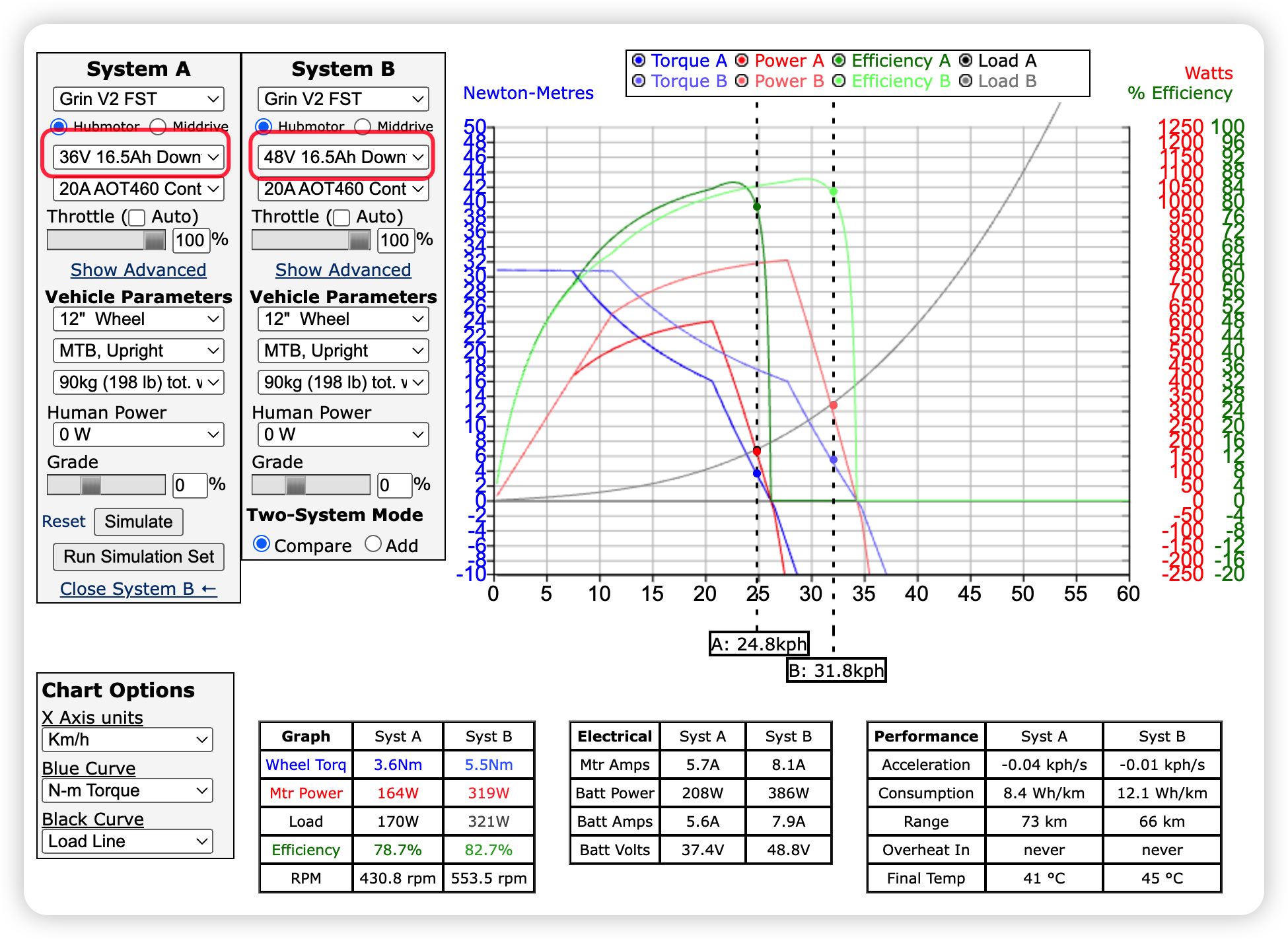
Now, let’s examine what happens when we increase the battery voltage from 36V (System A) to 48V (System B).
Following this adjustment, the maximum speed rises from 24.8 km/h to 31.8 km/h. However, the green curve illustrates that the efficiency of the motor at lower speeds is superior with the 36V system.
This scenario highlights the potential benefits of field weakening.
How Field Weakening Works in brushless DC (BLDC) Motors
- Principle: BLDC motors are typically controlled by varying the current through the motor windings using an Electronic Speed Controller (ESC). The ESC adjusts the current based on the rotor position, which is often detected by Hall effect sensors or through sensorless methods. In the field weakening phase, the ESC delays the timing of the current pulses to the windings relative to the rotor position.
- Implementation: To achieve field weakening in a BLDC motor, the controller deliberately advances or delays the commutation points (the points at which the current to a particular set of windings is turned off and on) beyond the optimal commutation point. This creates a situation where the magnetic field generated by the stator windings partially opposes the magnetic field of the permanent magnets in the rotor, effectively “weakening” the overall magnetic field experienced by the rotor.
- Effect on Speed: By reducing the magnetic flux interaction between the stator and rotor, the back electromotive force (EMF) that opposes the applied voltage is reduced, allowing the motor to spin faster than it would under normal commutation timing. This is useful for applications requiring operation at speeds higher than the motor’s rated speed.
Field weakening Pros and Cons
Pros
- Extended Speed Range: Field weakening allows BLDC motors to operate above their natural maximum speed, enhancing their versatility in applications requiring a wide range of speeds, such as electric vehicles and industrial machinery.
- Constant Power Operation: Beyond the base speed, field weakening enables constant power operation, allowing the motor to maintain power output even as speed increases, albeit with reduced torque.
- Improved High-Speed Efficiency: By enabling higher speeds without requiring proportional increases in voltage, field weakening can help maintain efficient operation across a broader speed range, particularly useful in battery-powered applications.
- Versatility: The ability to control speed and torque over a wide range significantly enhances the motor’s versatility, making it suitable for a variety of applications, from drones and electric bikes to precision industrial equipment.
- Reduced Need for Mechanical Gearing: By extending the motor’s speed range electronically, field weakening can reduce or eliminate the need for mechanical gear systems in some applications, simplifying the design and potentially reducing costs and maintenance.
Cons
- Complex Control Requirements: Implementing field weakening effectively requires sophisticated control algorithms and precise timing, increasing the complexity of the motor controller and the need for accurate rotor position sensing.
- Reduced Torque at High Speeds: While field weakening allows for higher speeds, it does so at the expense of available torque. This reduction in torque at high speeds can limit performance in applications requiring high torque.
- Increased Heat Generation: Operating in field weakening mode often results in higher current draw for a given power output, leading to increased heat generation that must be managed through effective thermal management.
- Potential for Controller and Motor Stress: The increased electrical stresses on both the motor and controller during field weakening operation can impact their reliability and lifespan, necessitating careful design and possibly leading to higher costs.
- Efficiency Trade-offs: Although field weakening can maintain efficient operation at higher speeds, the overall system efficiency can decrease due to the additional energy required to overcome the magnetic opposition and the potential for increased losses in the motor and controller.
The pros and cons lead us to a crucial lesson: The tradeoff for achieving higher speeds through field weakening is reduced torque and overall system efficiency, a significant limiting factor for electric vehicles where higher speeds result in increased load due to air resistance. This is why, in practical applications, field weakening can provide a speed boost of 5-10%.
[1] http://www.railway-technical.com/trains/rolling-stock-index-l/train-equipment/electric-traction-control-d.html
[2] https://ebikes.ca/tools/simulator.htm
[3] Addon: Understanding Everything about Hub Motor Drive Systems – Spezi 2020 Live Presentation
https://www.youtube.com/watch?v=c96n0Ma2rLY
Tahnks for the link to the motor simulator.
I heard this can overheat the motor and cause it to fail. Is this true?
Ich habe einen Bosh Motor der sich aber nur bis 27 km/h tunen lässt. Wie kann ich den hiermit schneller machen?